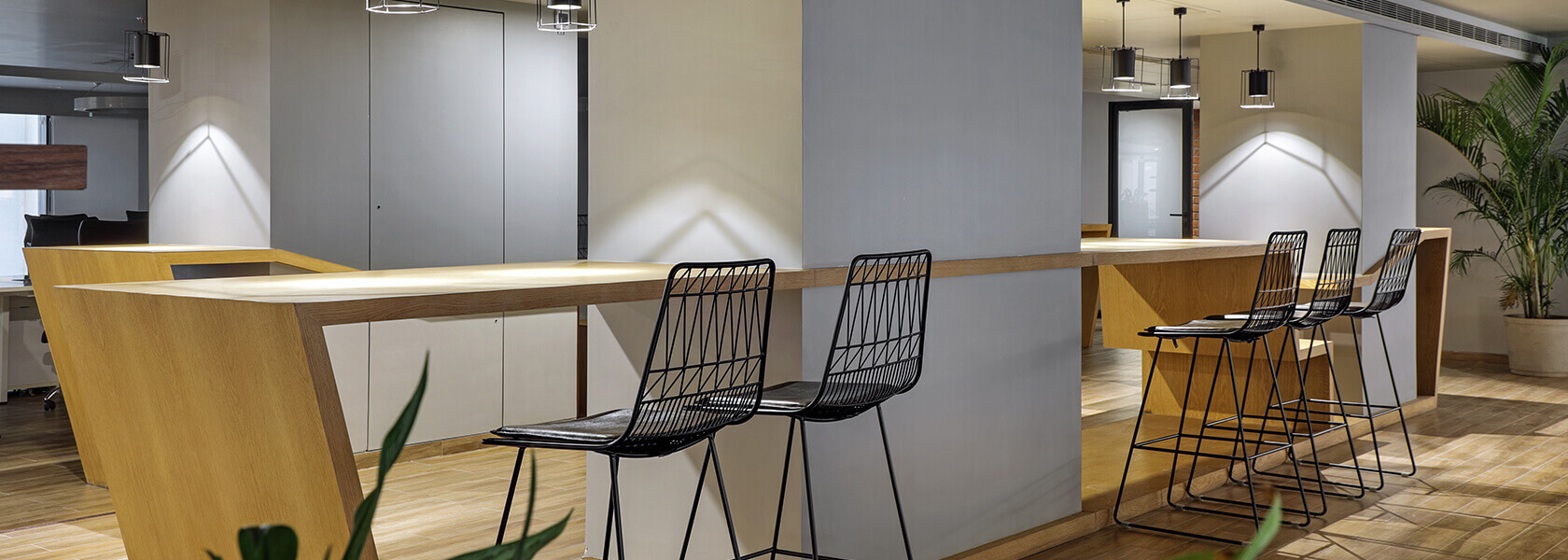
How IFS ERP helped a global manufacturer achieve 97% on-time delivery
- Industry: Manufacturing
Introduction
This global industrial manufacturing leader supplies critical components for industries ranging from energy to transportation, operating across 10 countries with a network of over 20 facilities. With rising demand, increased customization, and a leaner global supply chain, they were scaling fast—but their systems weren’t.
Each region and business unit had grown independently, adopting its own ERP or legacy tool. Finance in SAP. Manufacturing on Oracle. Procurement and warehouse in local systems. The result? Manual reconciliation, siloed data, and decision latency across the board.
Leadership knew that in a margin-sensitive, volume-driven business, slow systems don’t just cost time—they cost money.
The CFO led the charge for change. And the answer came in the form of one powerful, flexible platform: IFS ERP.
The Business Problem: Six Systems, Zero Unity
When business outgrows its systems, even the basics become bottlenecks. That’s exactly what happened here.
Fragmentation Was the Default:
- 6 legacy systems managing everything from inventory to financials
- Manual handoffs between departments, leading to data errors and version conflicts
- 10-day month-end close that delayed financial reporting and cash visibility
- Inconsistent on-time delivery metrics, depending on location or product line
What made it worse? No global view.
Executives couldn’t get real-time performance snapshots across plants or projects. Operational metrics were buried in spreadsheets. Forecasting was reactive. Cost overruns weren’t visible until quarter-end. And finance had to work overtime just to generate basic reports.
The tipping point came when a critical order for a high-profile aerospace client was delayed—not due to capacity, but because two systems couldn’t talk to each other. That delay cost the company the next contract—and sparked the urgent need for transformation.
Our Solution: One Real-Time Platform—IFS ERP
IFS ERP was selected after an extensive evaluation of Tier-1 vendors. What set IFS apart? Its modular agility, deep industry fit, and ability to consolidate multiple entities on a single platform—without losing local flexibility.
Tntra’s IFS consulting team partnered closely with the CFO’s transformation office to deliver a phased, high-impact rollout across regions and functions.
Implementation Priorities Included
Unified Chart of Accounts and Global Ledger
Consolidated financials across geographies, with local compliance built-in
Integrated Manufacturing & Supply Chain
Real-time production tracking, MRP, inventory visibility, and supplier coordination
Automated Procure-to-Pay & Order-to-Cash
No more spreadsheets, email chains, or manual reconciliation
Embedded KPIs and Dashboards
Role-based analytics for finance, operations, and executive teams
Global Standardization with Local Agility
Plants retained necessary localization, while corporate gained global control
Using IFS’s agile deployment methodology, the company went live in 18 months—across 20 sites, 5 countries, and thousands of users.
Outcomes: Measurable Business Impact at Every Level
Within the first year of going live on IFS ERP , the company saw a transformation across finance, operations, and customer delivery.
Key Business Outcomes:
Month-End Close in 3 Days
The global close cycle dropped from 10 days to just 3—freeing up finance teams, improving cash visibility, and enabling faster, better decisions.
- Financial statements now available on day 4
- Forecasting accuracy improved by 30%
- Real-time cash and margin visibility
97% On-Time Delivery
With integrated production scheduling and inventory control, order fulfillment became predictable and reliable.
- 97% on-time delivery rate globally
- Reduced expedited shipping costs by 22%
- Better customer retention and repeat orders
5-Point EBITDA Uplift
Unified operations and reduced manual overhead translated directly into bottom-line growth.
- Reduced supply chain waste and duplicate efforts
- Optimized procurement and vendor terms
- Improved project costing and profitability tracking
A Single Source of Truth Across the Enterprise
Whether it’s a factory manager checking materials, a regional CFO validating forecasts, or the CEO looking at margin trends—all are now seeing the same real-time data.
- Role-based dashboards with drill-downs to transactions
- Cross-department collaboration based on shared metrics
- Elimination of 80% of manual reporting
Future-Ready and Scalable
IFS ERP’s modular nature means the company can continue evolving—whether through M&A, new market entry, or digital service offerings.
- Integrated with IoT for machine-level visibility
- Laid the foundation for predictive maintenance
- Ready for future cloud migration
IFS ERP wasn’t just about technology—it became the foundation for profitable, predictable, and scalable growth.
Want to explore IFS ERP for your manufacturing business?
Talk to Tntra’s IFS specialists and start your transformation today.